Adopting a process approach to optimise performance
Process… a term that can be frightening, as it may suggest images of tasks to be carried out in a quasi-mechanical way, as in the days of Taylorism, with notions of rigid organisations, strict rules to be followed, and even rationalisation or streamlining.
However, a company and/or an organisation, is made up of a set of processes which defines it.
DEFINITION OF A PROCESS ACCORDING TO THE INTERNATIONAL STANDARD ISO 2001 (2000’S VERSION) [1] :
A set of correlated or interactive activities that transforms input elements into output elements. In his book “Achieving Total Quality Management: A Program for Action”, Michel Périgord goes further by describing a process as “a succession of tasks carried out with the help of resources such as staff, equipment, materials, information and procedures. The expected end result is a product. It presupposes measurable inputs, added value, measurable outputs and the possibility of being repeated.”
Processes, what about them?
Controlling business processes is about being aware of how products (or services) are manufactured (or delivered), from the customer’s request to the purchase of raw materials, invoicing and delivery.
Firstly, it requires an understanding of how value is created in the company. As seen in the definition, this involves identifying activities that do not add value, that the customer is not willing to pay for, and which therefore can be dropped or outsourced.
Secondly, it also means knowing which skills and what knowledge are essential to the performance of the company’s activities, and how to better capitalise on them.
Finally, it also means being flexible and responsive. This helps to adapt and react very quickly when a malfunction occurs. In fact, by breaking down and organising the tasks, that lead to the products or services it offers, in a logical sequence, the company maps out all its activities and can thus identify the critical links within the organisation.
The advantage of using the process approach is that you start with the end goal (the product or service) in mind and work your backwards through the various stages, describing the stakeholders, their roles and interaction.
Why use processes?
The findings that can emerge from such an analysis are multiple, and that can lead to various measures and actions, are:
FINDINGS FROM A PROCESS ANALYSIS
EXAMPLE OF CRITICAL SITUATIONS
EXAMPLES OF WHAT CAN BE DONE ABOUT IT
Same tasks carried out in multiple parts of the company
In the case of a merger, or when there are remnants of a past restructuring (departments have been reorganised, but the old ways of working have been retained)
Rationalisation, sharing a skill and or responsibility (e.g.: accounting) between several departments…
The realisation of the product/service depends on just a few people
The company does not focus on its flagship product or core business and is losing skills
Transfer of know-how to avoid being left without a competent person in case of departure or illness
Unstructured information flow
If a problem arises, an email is sent to a whole list of people in the hope that one of them will feel that they are the one concerned…
Reorganisation of communication flows, roles and responsibilities, then documentation and communication of the resulting streams
Redundancy of tools addressing the same needs
When the tool that is imposed by management does not meet the needs of users, they then develop their own alternative solutions (Excel tables, Access databases, etc.)
Assessment of needs, workflows, technical constraints, etc. Then, drawing up precise functional specifications and choosing of an adhoc tool. Involvement of users at all stages of the process, as well as on-the-job support during implementation
“Orphan” tasks: embedded in a process without being aware of their impact on the organisation
A task is carried out by a single employee, who knows the details of his or her activity perfectly well, but whose presence has become essential to ensure that this task is carried out. The company sometimes realises several weeks after the departure of the employee that the activity is no longer being carried out and that it is missing from its organisation (e.g.: updating a database)
In the event of retirement for example: transfer of know-how through mentoring several months before departure and carry out an exit interview to detect any unregistered practices
Lack of information about how the task is performed and how it is linked to other tasks
The service is provided, but the know-how is not documented
Documentation of the necessary steps to produce the product/service, in order to capitalise on the knowledge and improve knowledge management
The identified dysfunctions will lead to the implementation of actions to improve (or optimise) the processes. Process improvement is one of the essential concepts of quality management.
The challenge is twofold:
- to improve the quality of the company’s products/services
- to refine the way the company operates by limiting compartmentalisation, by making it easier to anticipate and communicate, and by giving responsibility to the stakeholders involved in the process.
A company therefore operates according to processes, which are sequences of correlated activities, involving resources and skills at different levels of the company, with the aim of transforming information or raw materials into a finished product or service.
Process analysis… for a better use of its information systems
Let’s take the case of corporate information systems, which, due to the evolution of information technologies and their ever deeper penetration into business processes makes their control more and more mandatory. The risks associated with them affect the survival of companies and consequently the interests of their shareholders.
During the 2000s, cases such as the Enron scandal, or other financial scandals, suddenly made people aware that information systems, which are the backbone of these large groups, are driven by extremely complex processes that are not controlled by people.
In the United States, lawmakers have therefore created laws that require companies listed on the New York Stock Exchange to strengthen control of their financial processes and, consequently, of the related IT processes: these are the Sarbanes Oxley Act (SOX) and the Homeland Security Act. Their application to the control of information systems has resulted in the adoption of standards such as ITIL (Information Technology Infrastructure Library) or COBIT (Control Objectives for Information and related Technology).
Therefore, controlling business processes also means creating value by replacing activities that were previously carried out by humans with “IT services”, provided that you never allow yourself to be(come) overwhelmed by the processes put in place.
[1] Reference: ISO 9001 version 2000 standard: the approach to problems through process improvement.
WANT TO RECEIVE OUR LATEST THOUGHT LEADERSHIP CONTENT?
Related posts
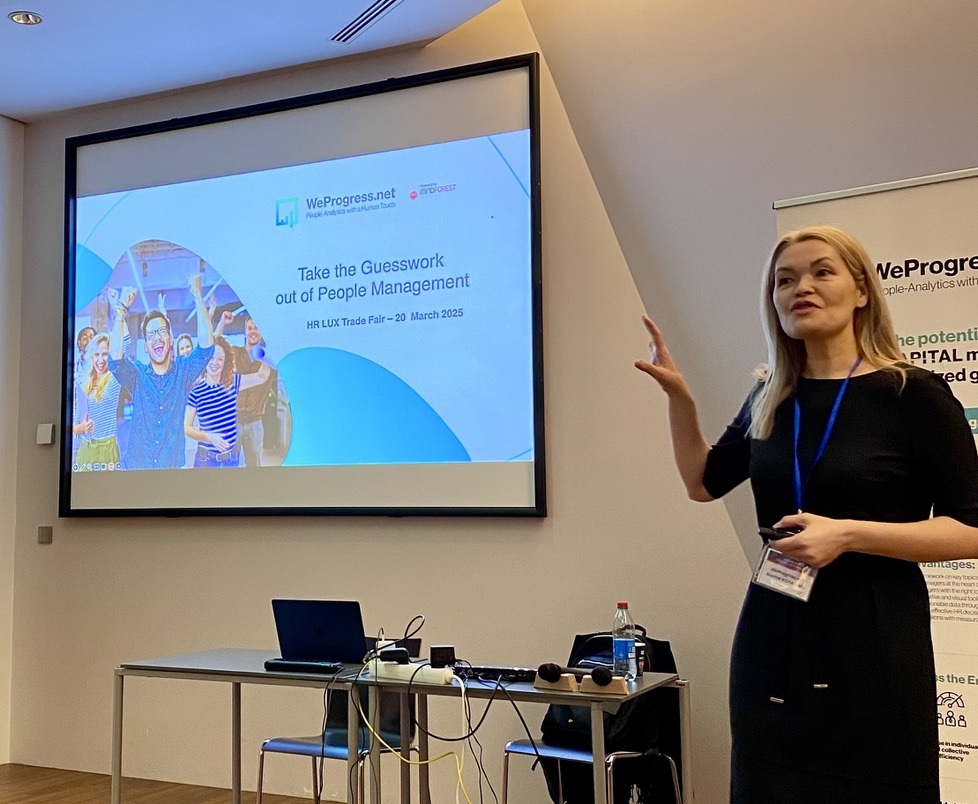
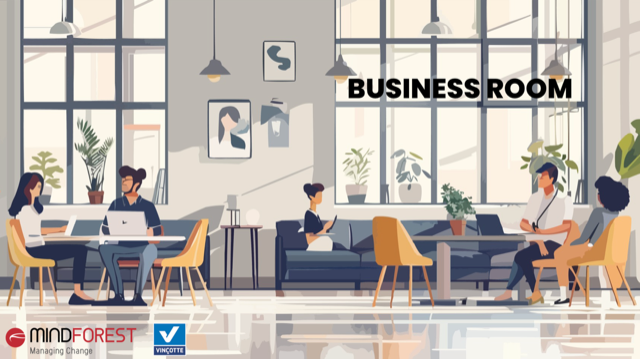
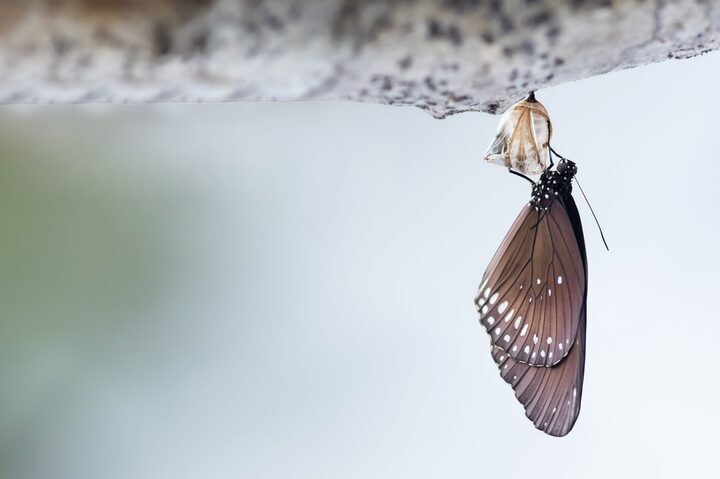
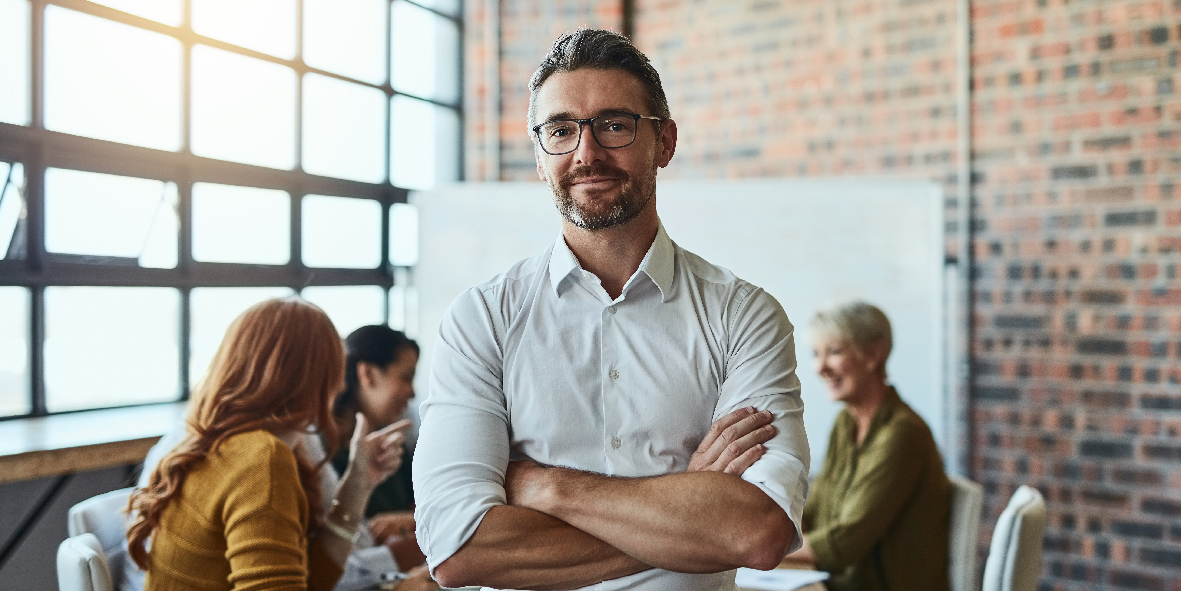
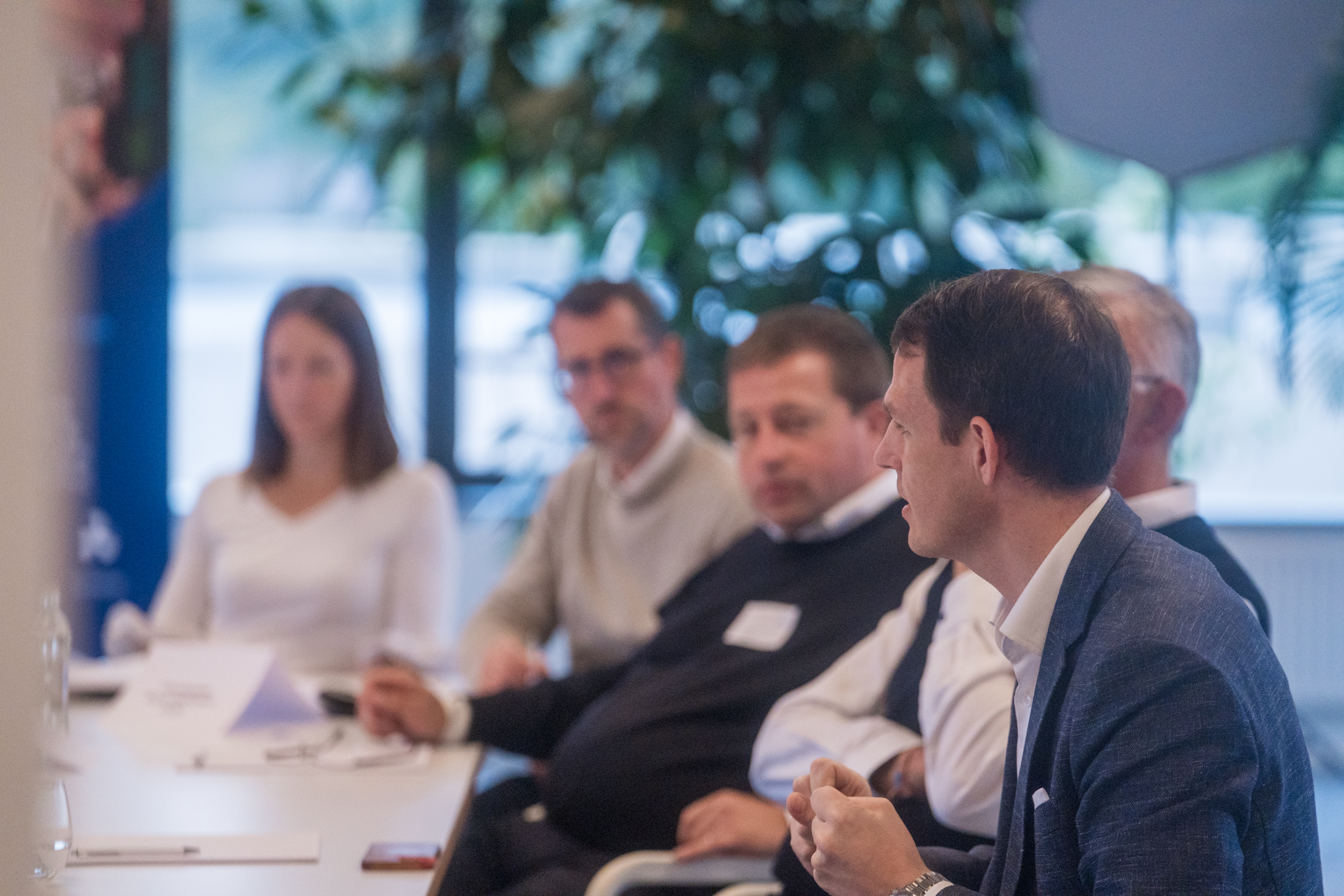